What is dynamic balancing?
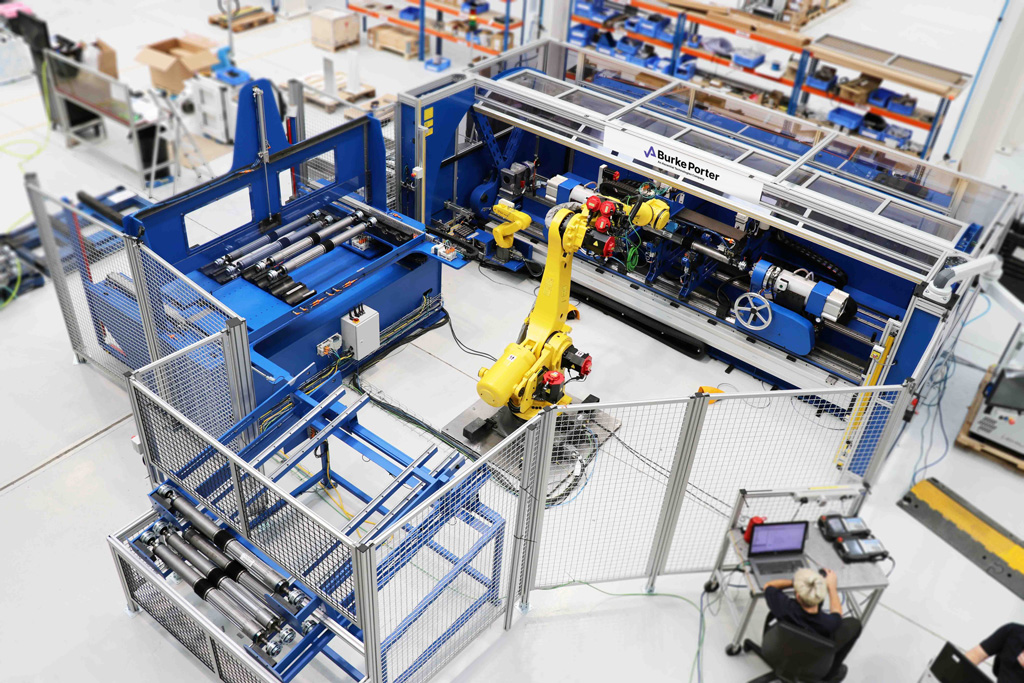
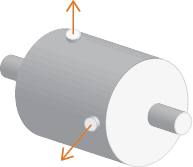
What is dynamic balancing?
Dynamic balancing is a method used to correct unbalanced rotors to reduce noise and vibration and improve quality and life expectancy of machinery. Unbalance is a result of uneven distribution of mass around the axis of rotation. Balancing is achieved by rotating the component at speed and using measuring equipment to find heavy points that are causing unbalance. When the unbalance positions are known, weight can either be removed at this location or added to the opposing side to balance it.
Dynamic unbalance is typically a combination of axial and radial forces also known as couple and static unbalance, causing the mass axis to be different to the rotational axis. Dynamic unbalance is corrected in 2 or more planes and is common for components like multi stage pumps, crankshafts, and turbines.

What is couple balancing?
Couple unbalance is an axial force that occurs when a rotating mass has two equal unbalance forces that are situated 180° opposite each other. A system can be statically balanced and still have a couple unbalance. Couple unbalance occurs frequently in elongated cylindrical rotors and is usually corrected in 2 planes.
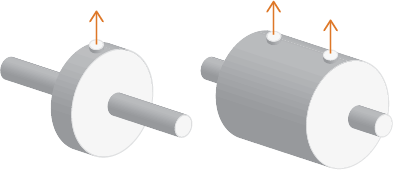
What is static balancing?
Static unbalance is parallel to the rotational axis and produces a radial force on the rotor. Unbalance is corrected in 1 axial plane and can be measured using both rotating and stationary balancing machines.
Static balancing is used for disc shaped components like small fly wheels, pump rotors, brake discs and clutches.
Benefits of static and dynamic balancing
- Less noise
- Less vibration
- Comfort
- Efficiency
- Improved safety
- Reduced downtime
Unbalanced rotors want to rotate around their mass centre axis instead of their rotational axis. The bearings prevent this movement, but cause vibration of the rotor, bearings and other parts attached. This results in unnecessary wear on all components in the machine and can shorten its operational lifespan and cause more frequent breakdowns.
Noise and vibration produced by an unbalanced rotor can be directly connected to comfort and quality, especially in the automotive industry. Unbalanced car components will result in an uncomfortable and noisy ride which could also reduce the value of the vehicle and its reliability.
What are balancing limits?
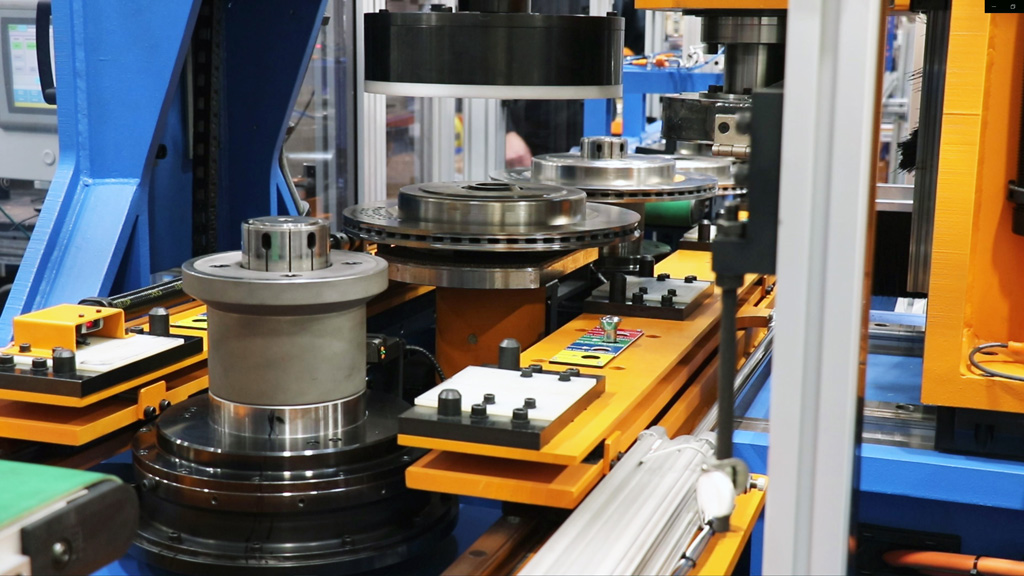
What are balancing limits?
Balancing limits indicate acceptable amounts of unbalance in rotors. Manufacturers typically specify acceptable tolerances for their components based on their testing. However, international standards (ISO 21940) exist and state balance quality G grades for different rotor types that can be used to calculate balance tolerances. G Grade 40 is a typical balancing limit for car wheels while rotors such as small electrical armatures require higher accuracy so are typically balanced to Grade 2.5.
Units of unbalance
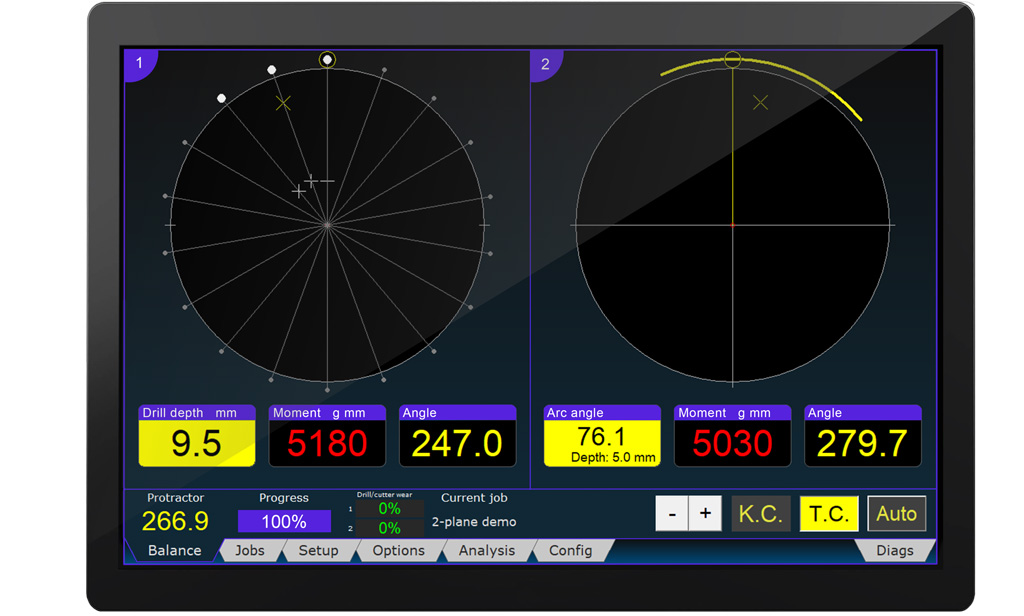
Units of unbalance
The units of unbalance are mass times radius, for example: a weight added to a certain position on the part being balanced would shift the mass axis into the running axis and therefore be in balance. The weight of correction multiplied by the applied radius will give an unbalance unit. For metric measurement the units will be gram-millimetres (gmm) or for large rotors, gram-centimetres. The Imperial equivalent will be gram-inches or ounce-inches. This weight (mass) would be applied at a radius from the running centre at the light position.
How to measure static and dynamic unbalance
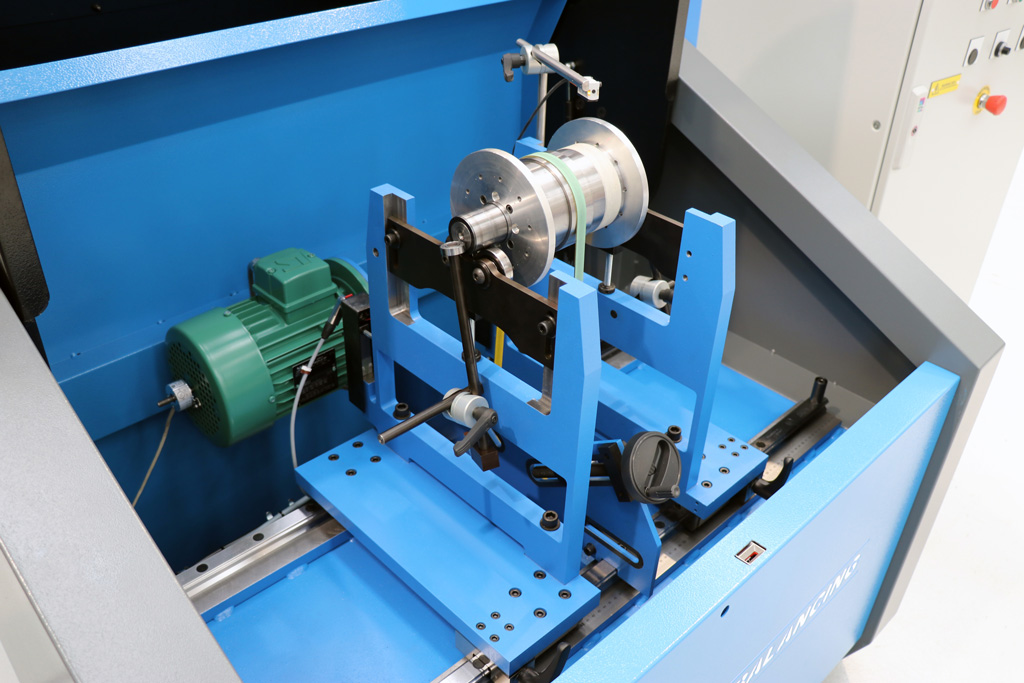
How to measure static and dynamic unbalance
We use balancing machines to precisely measure an unbalanced rotor and determine the exact angle and amount of unbalance. Sophisticated balancing software displays the data clearly, indicating correction positions on the rotor and the amount of weight to be added or removed. Different balancing machines are used depending on the rotor type, for example a disc shaped rotor that requires single plane / static balancing will typically be balanced on a vertical machine where the rotor axis is in a vertical position during measurement. A horizontal balancing machine can be used to measure couple and dynamic unbalance in rotors where the length is proportionally greater than the diameter. The rotor axis will be in a horizontal position on this machine.
How to correct an unbalanced rotor
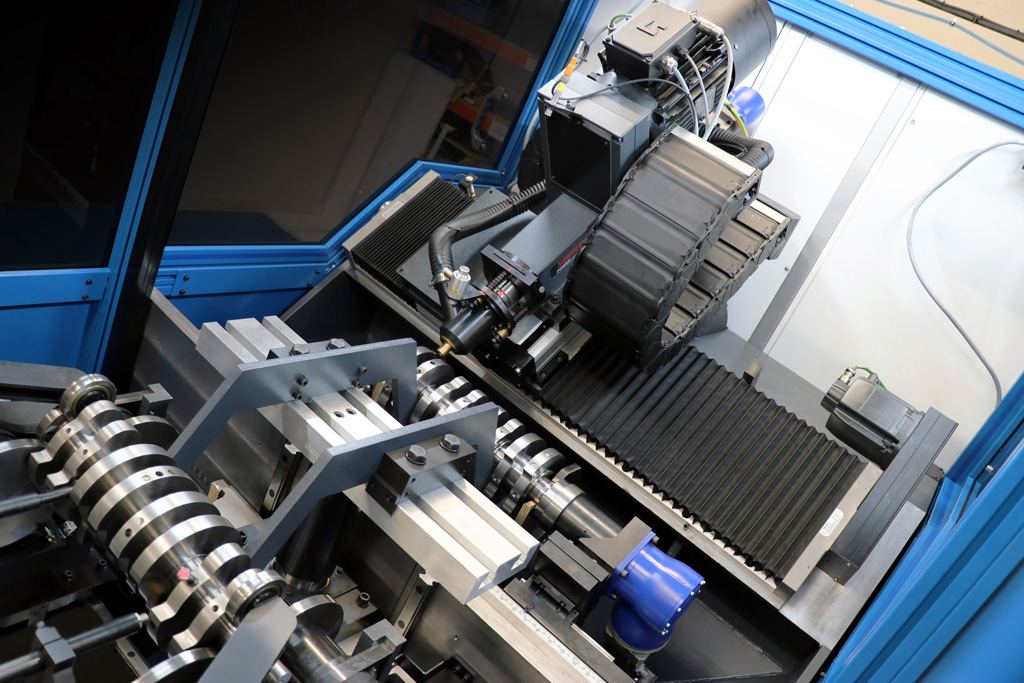
How to correct an unbalanced rotor
After we have identified the unbalance positions on a rotor using a balancing machine, we apply correction by either removing material from the heavy position or adding material to the light position. Typical removal methods include milling, drilling and grinding while methods of adding weight can include welding or bolting weights to the part or using weighted clips.
Types of rotors
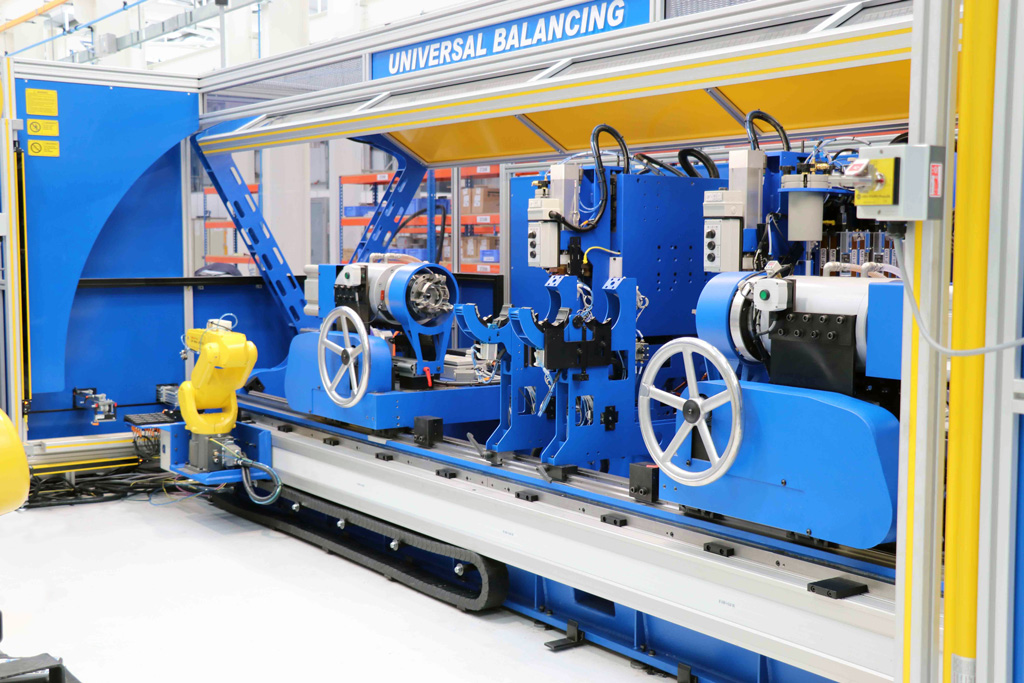
Types of rotors
Rotors fall into two groups. One is where the rotor is rigid and does not deflect up to and including the operating speed. The other group comprises flexible rotors that “bow” up to the operating speed. The first deflection seen is a “skipping rope effect” which means the centre of the rotor at speed moves out from its rotational axis, causing high static unbalance.
Balancing rigid rotors
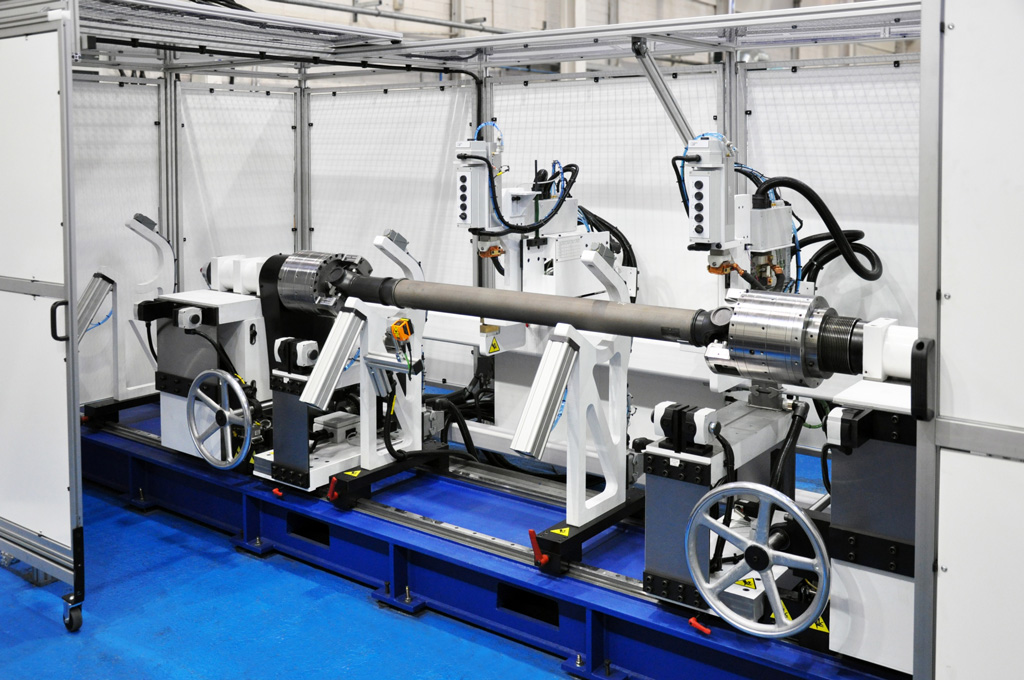
Balancing rigid rotors
Because unbalance exists in a component even when stationary, rigid rotors can be balanced at a low speed, just enough to produce a centrifugal force to register the unbalance.
Balancing flexible rotors
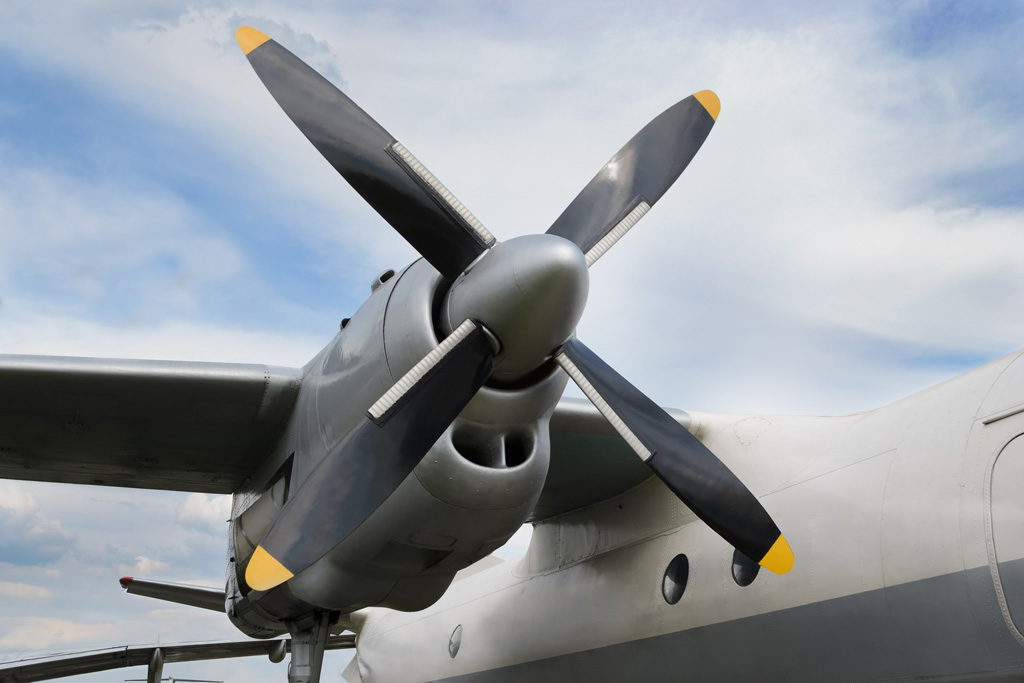
Balancing flexible rotors
This type of rotor is balanced at a low speed where the rotor does not flex. Correction for unbalance is made, then the speed is gradually increased, and the unbalance is corrected in stages until the rotor’s operating speed is reached.
Static and dynamic balancing of your parts
We provide static and dynamic balancing services to repairers and large companies across UK and Europe who require crankshaft balancing, fan balancing, shaft balancing, and much more. We have the equipment and experience to balance almost any rotating component quickly and to a high standard.
We use several vertical and horizontal balancing machines from the balancing technology experts Burke Porter to provide you with guaranteed high quality precision balancing solutions for your parts.
How can we help you?
If you know what you want, use the Free Quote button to get started.
If you need a chat, fill out the form below and our experts will be in touch.